Fonderie Gravitaire
Depuis le tout début de notre activité nous produisons des petites et moyennes séries par gravité. Le groupe est équipé de 17 machines hydrauliques gravitaires au Portugal. L’aluminium en fusion est versé en gravité à la louche manuelle dans un outillage métallique hydraulique.
Les pièces qui en sortent sont de grande dimension et ont une très forte résistance.
Un projet ?
Fonderie à injection Aluminium
L’aluminium est poussé automatiquement dans le four et injecté par un piston dans le moule. Ce procédé permet d’obtenir des pièces plus fines et plus complexes qui conservent une grande résistance mécanique grâce au compactage.
Le groupe possède 9 presses à injection dont la puissance varie de 150 à 420 Tonnes. Elles sont réparties entre l’Espagne et le Portugal.
L’injection permet d’avoir des pièces à l’aspect plus esthétique mais tout aussi résistantes.
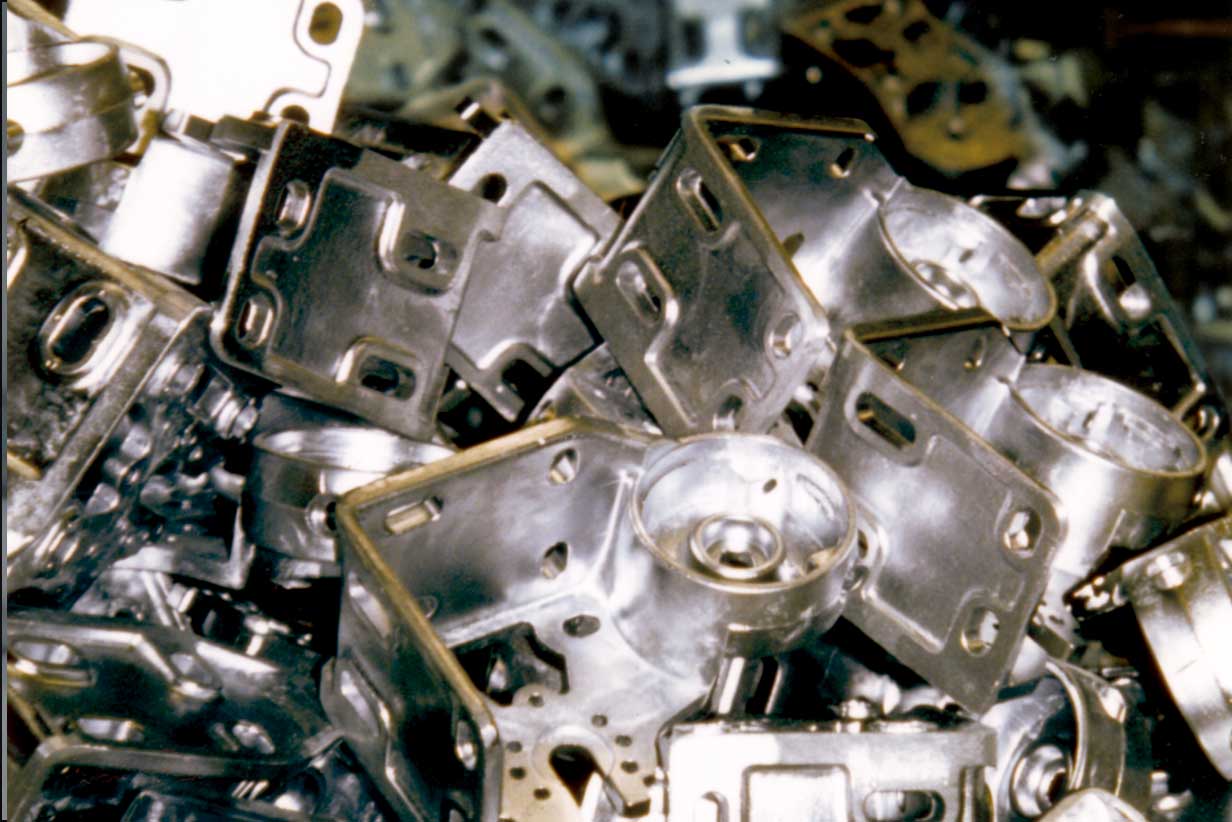
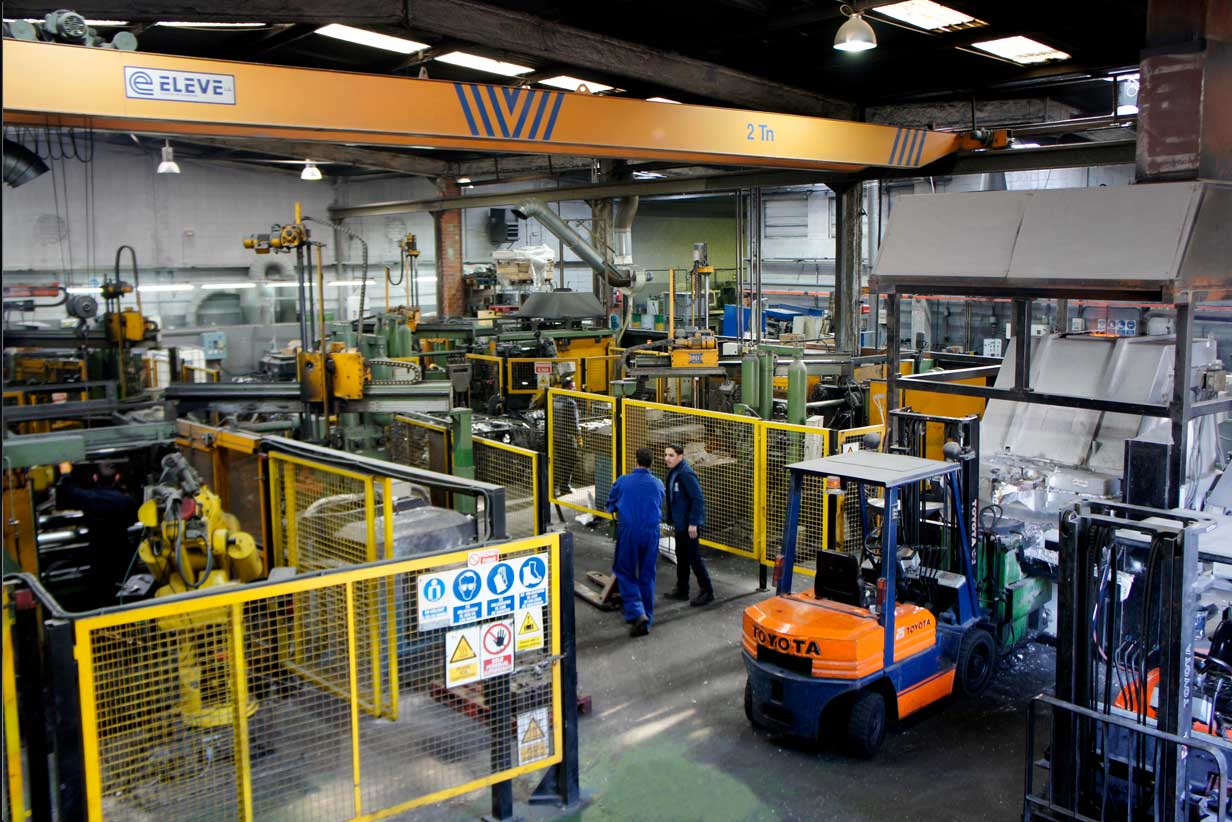
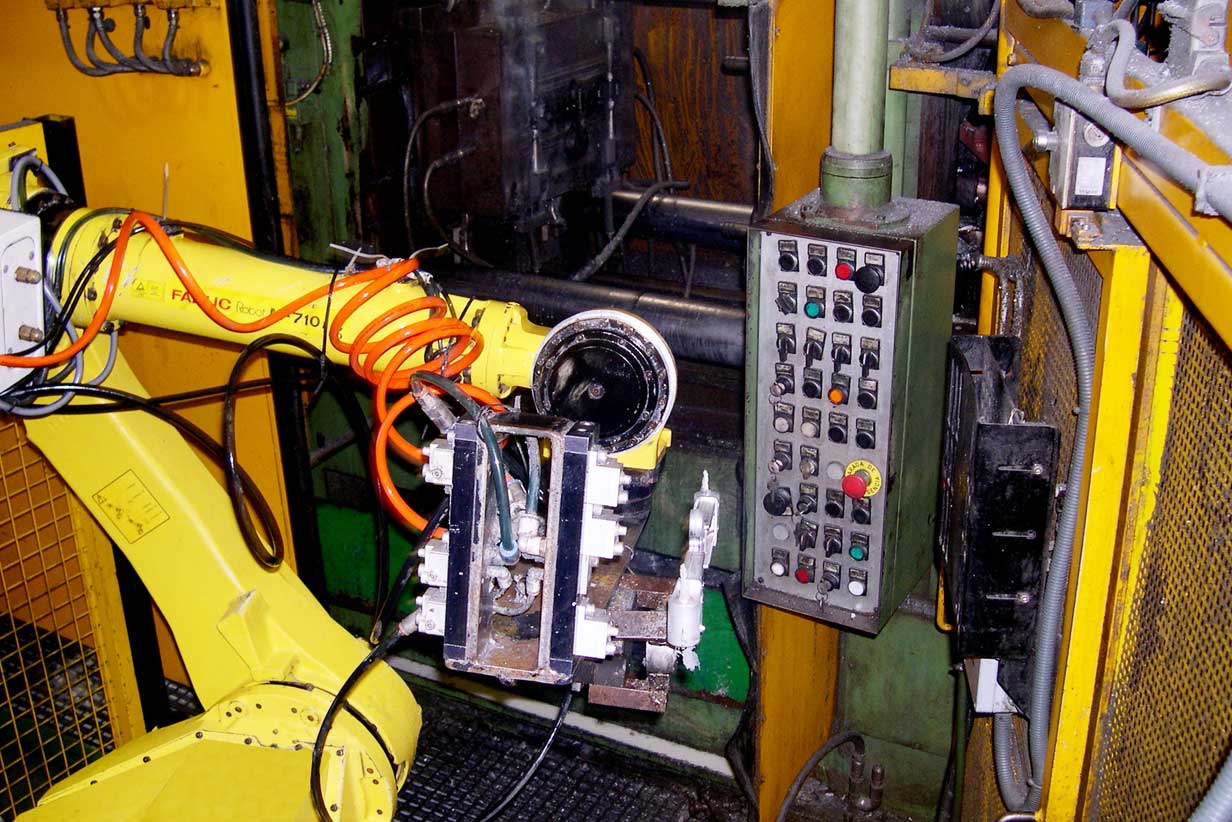
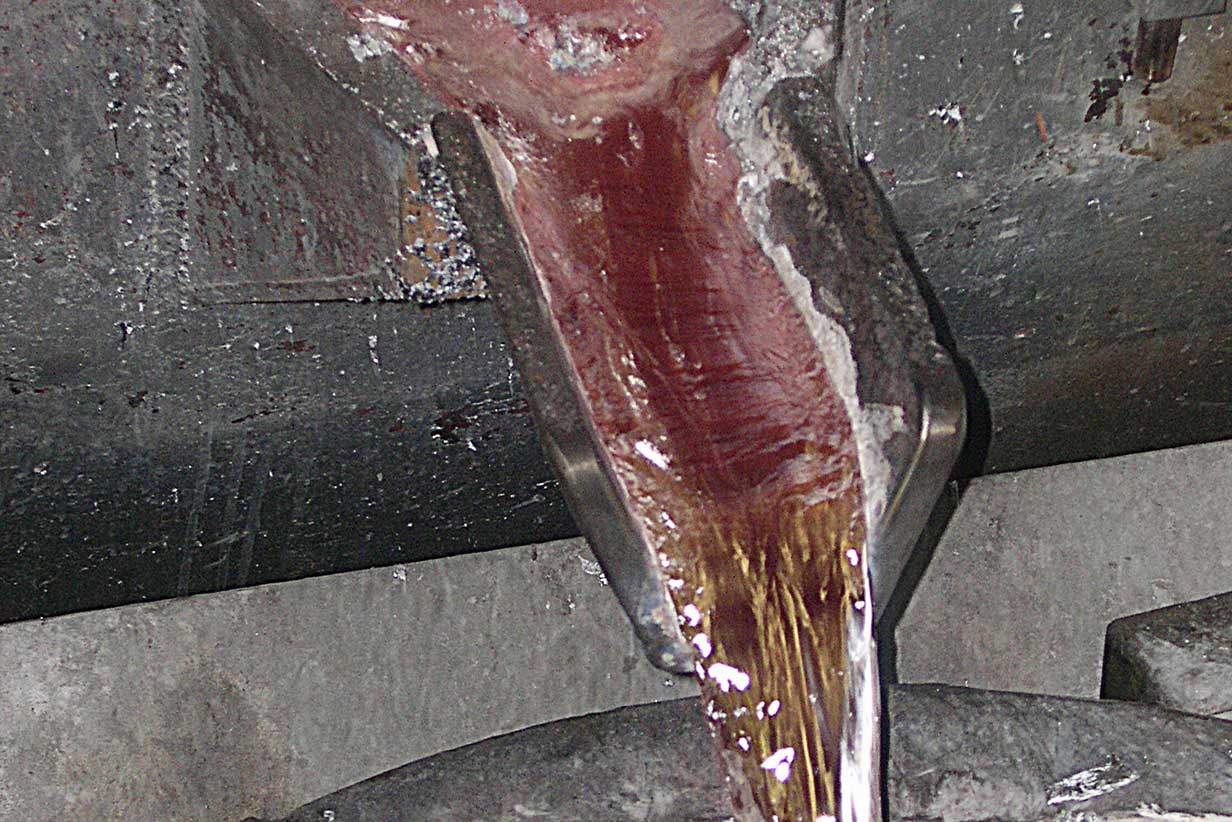
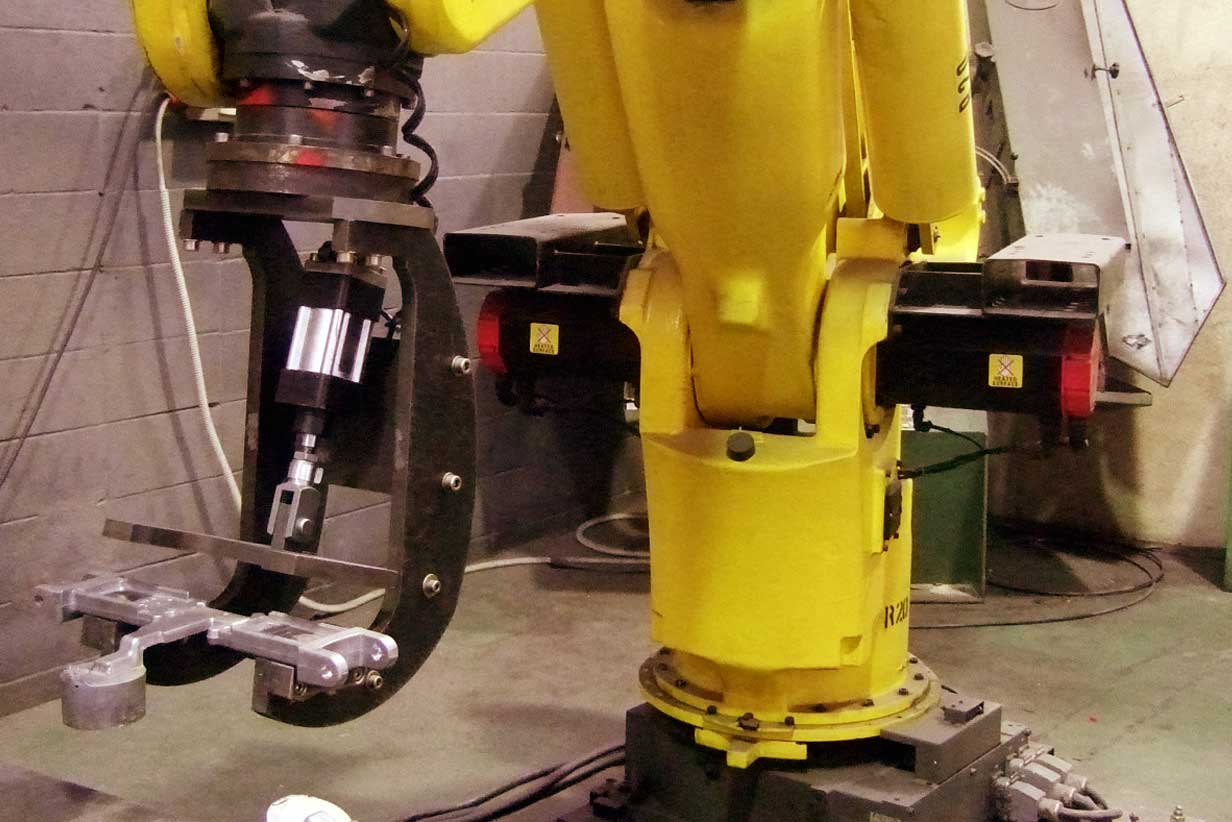
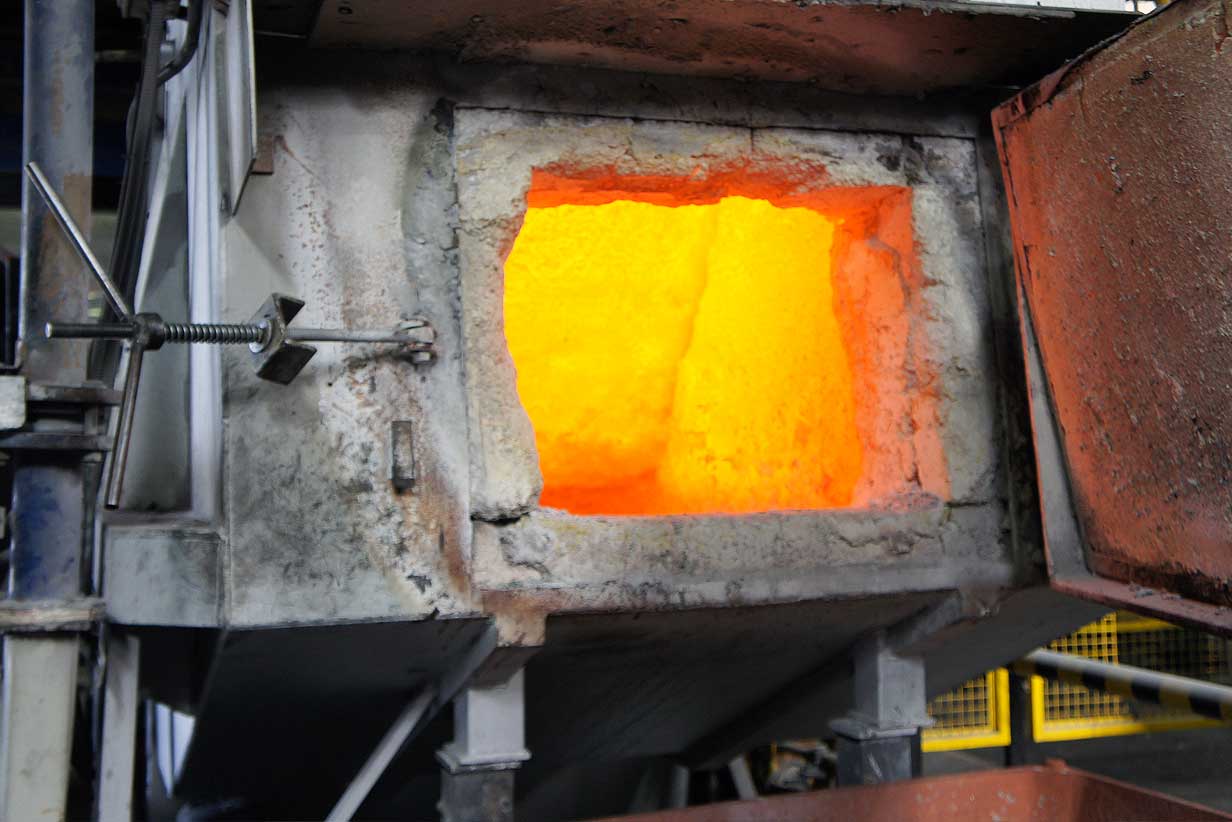
Injection Zamak
Le Zamak est un alliage dont le principal composant est le Zinc. Le process de fabrication des pièces est le même que pour l’injection aluminium à la différence que tous les composants de la presse doivent être maintenus chauds.
L’avantage du zamak est de bénéficier d’un cycle de production plus rapide. Il permet une reproduction de tous les détails de la pièce qui n’aura pas besoin d’être mécanisée.
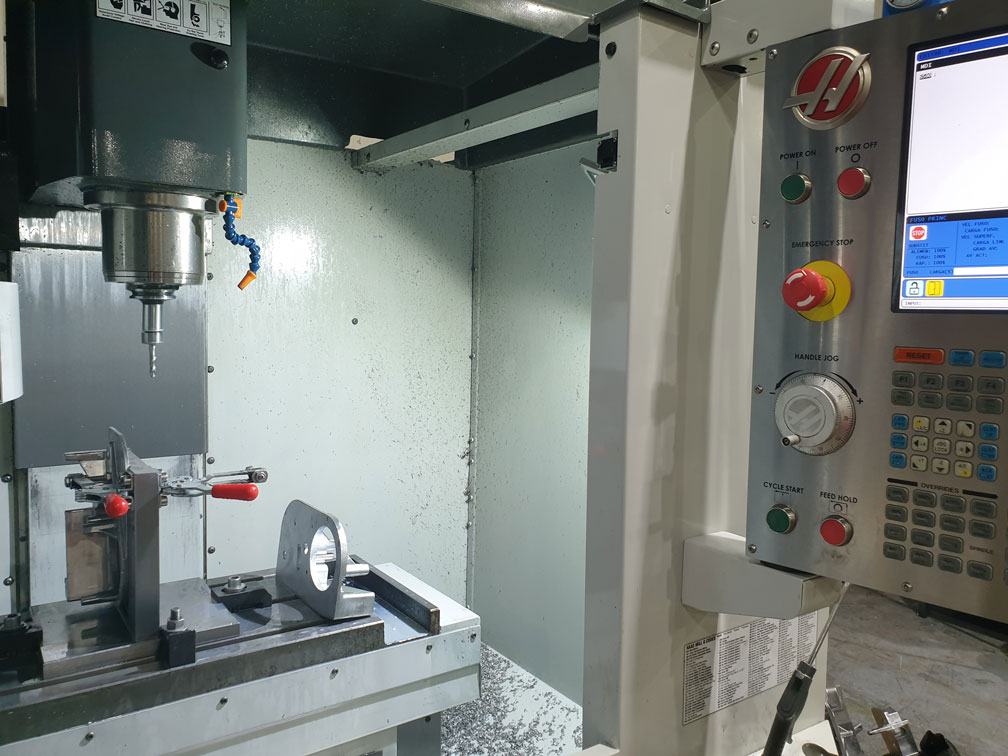
MÉCANISATION
Les ateliers de mécanisation sont présents dans toutes les unités de production.
Pour répondre aux exigences de nos systèmes, certaines pièces à la sortie de fonderie doivent passer par des centres d’usinage pour une grande précision de mécanisation.
À cette étape nous vérifions aussi la visserie et la finition des pièces avant le traitement et ou laquage.
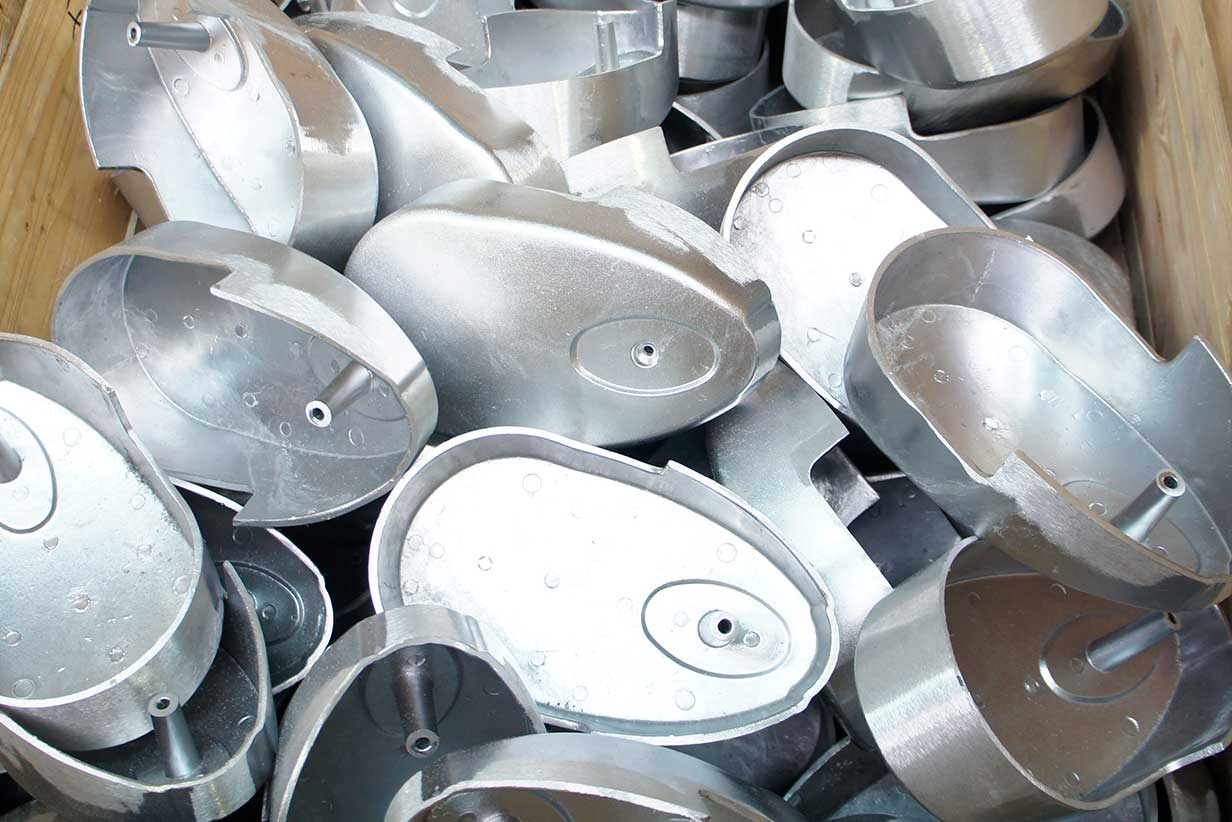
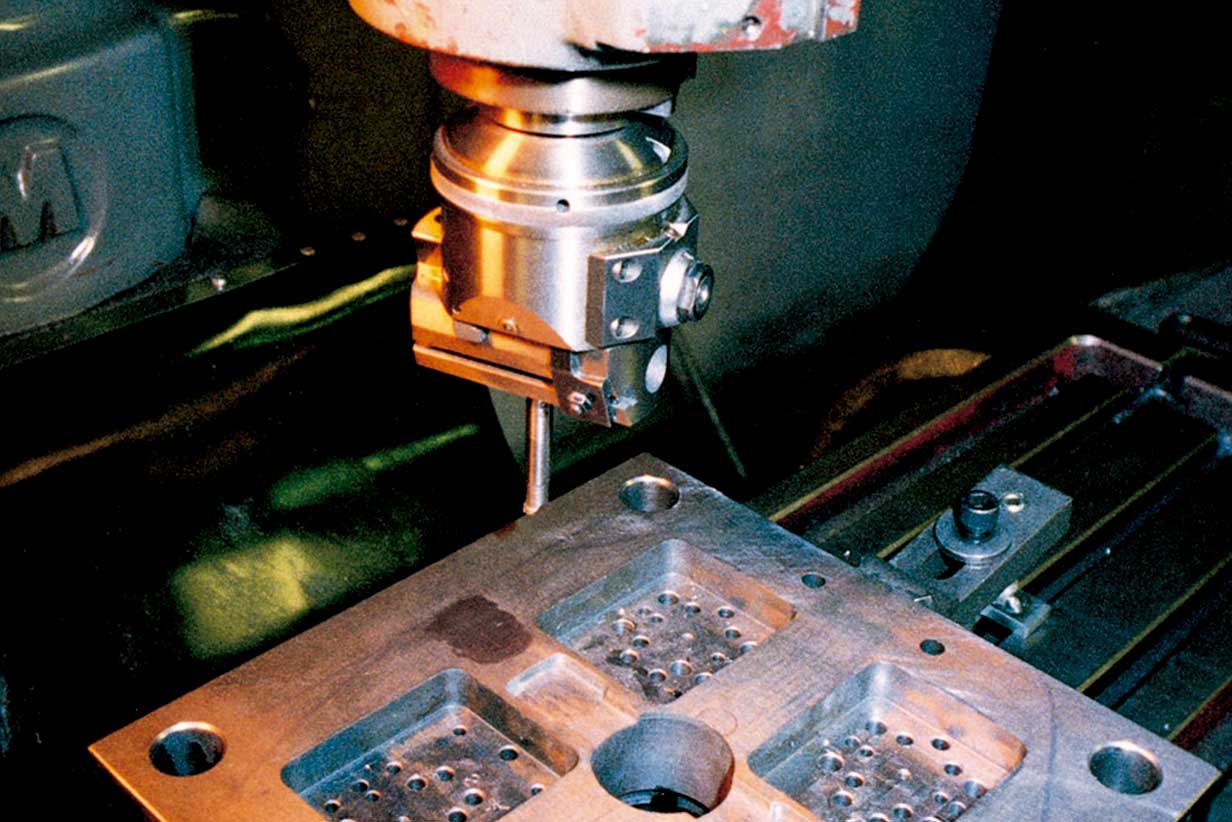
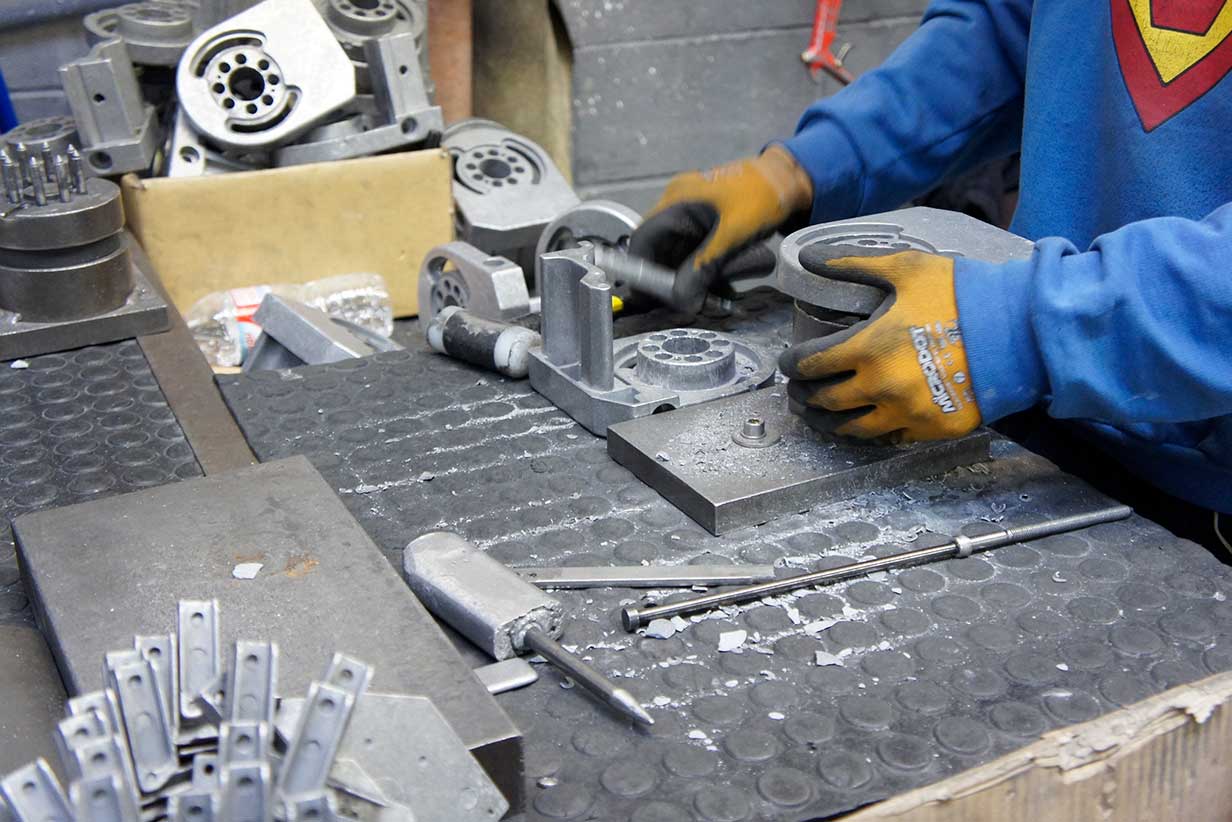
NOUVEL ALLIAGE ALUMINIUM
Meilleure résistance des pièces
Toujours dans un esprit d’amélioration de la qualité de nos produits, nos fonderies aluminium utilisent désormais un nouvel alliage aluminium pour la fabrication des pièces de fonderie.
Cet alliage contient moins de fer que les alliages utilisés traditionnellement mais il est compensé par l’augmentation de la teneur en manganèse (métal de transition ressemblant au fer). L’intérêt étant de fournir un matériau alliant résistance et ténacité, grâce à des grains d’une extrême finesse.
Ainsi, l’alliage augmente la résistance mécanique et à la corrosion de nos pièces.
Après avoir réalisé de nombreux tests comparatifs, nous avons constaté une meilleure résistance de nos pièces de fonderie avec le nouvel alliage 35% à 40% de résistance supplémentaire par rapport à notre alliage traditionnel.
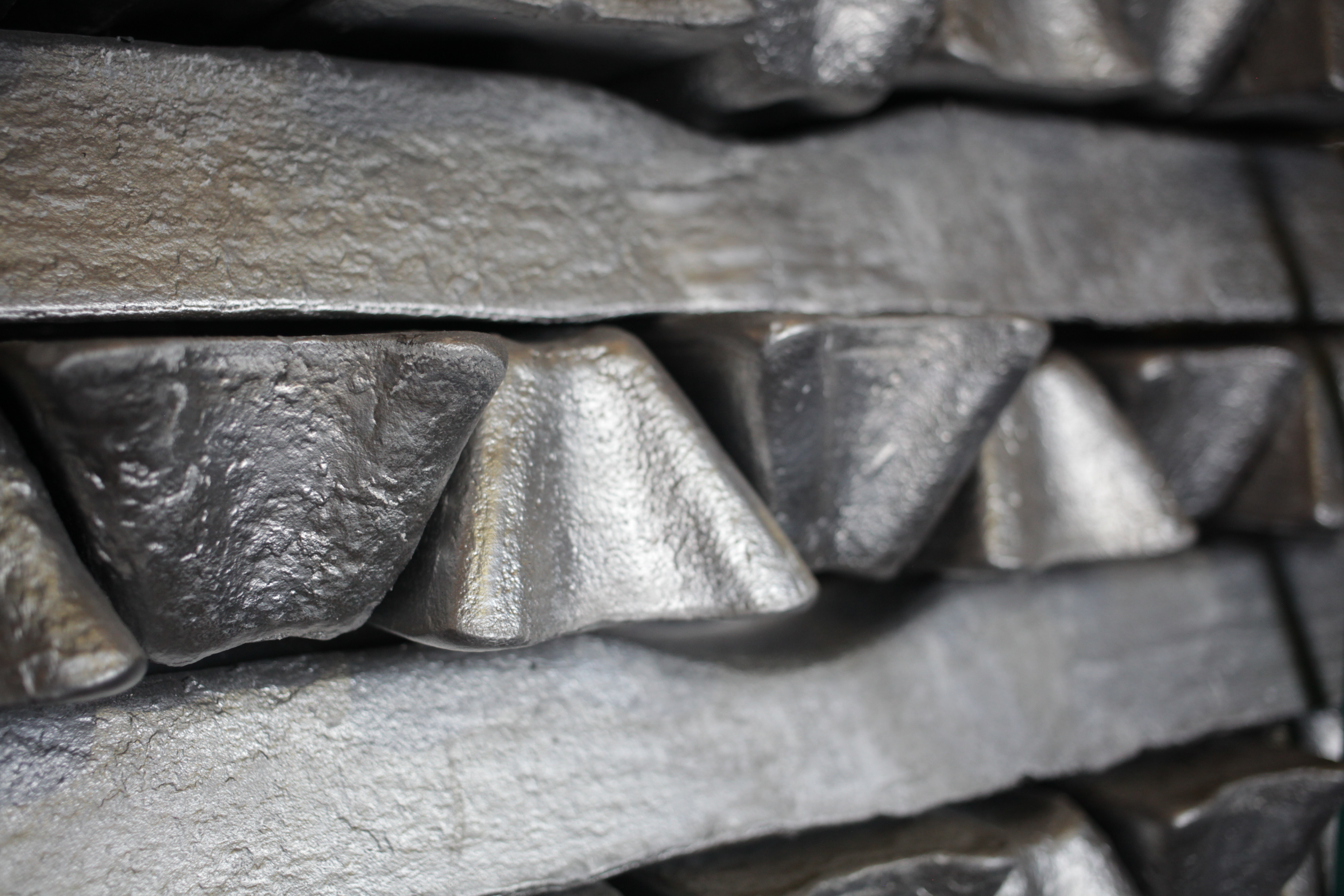