Gravity Foundry
Since the very beginning of our activity we have been producing small and medium series by gravity. The group is equipped with 17 hydraulic gravity machines in Portugal. The molten aluminum is poured by gravity with a manual ladle into a hydraulic metal tool.
The parts that come out are large and have a very high resistance.
Injection molding Aluminum
The aluminum is automatically pushed into the furnace and injected into the mold by a piston. This process makes it possible to obtain thinner and more complex parts that retain high mechanical strength thanks to compaction.
The group has 9 injection presses with a power range from 150 to 420 Tons. They are divided between Spain and Portugal.
Injection molding makes it possible to have parts with a more aesthetic appearance but are just as resistant.
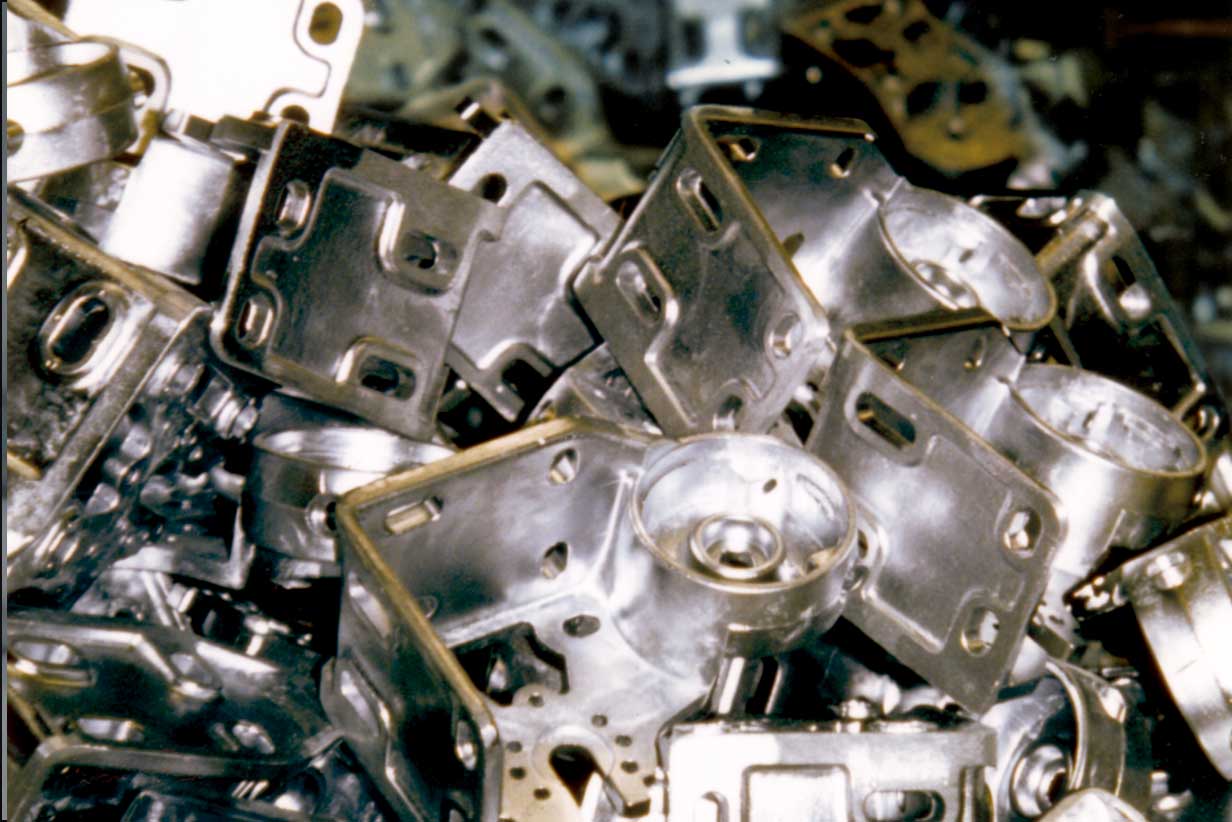
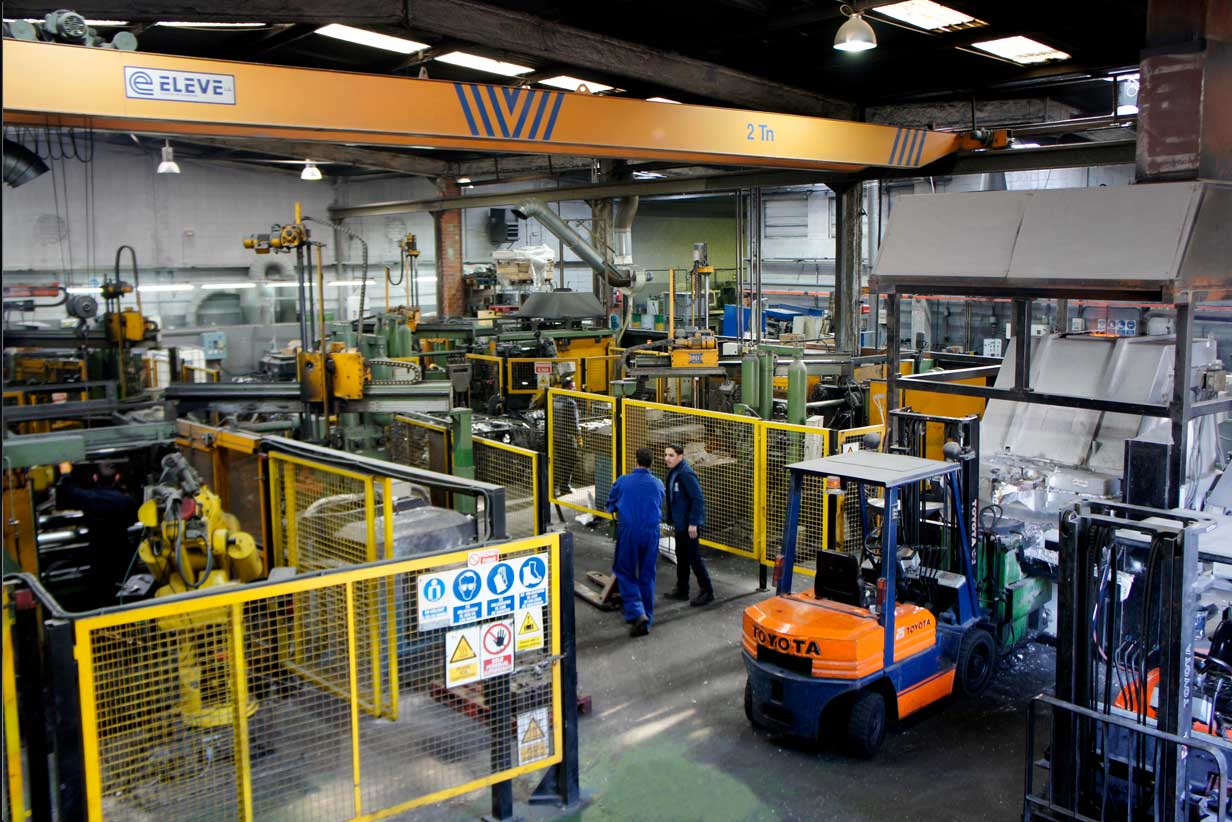
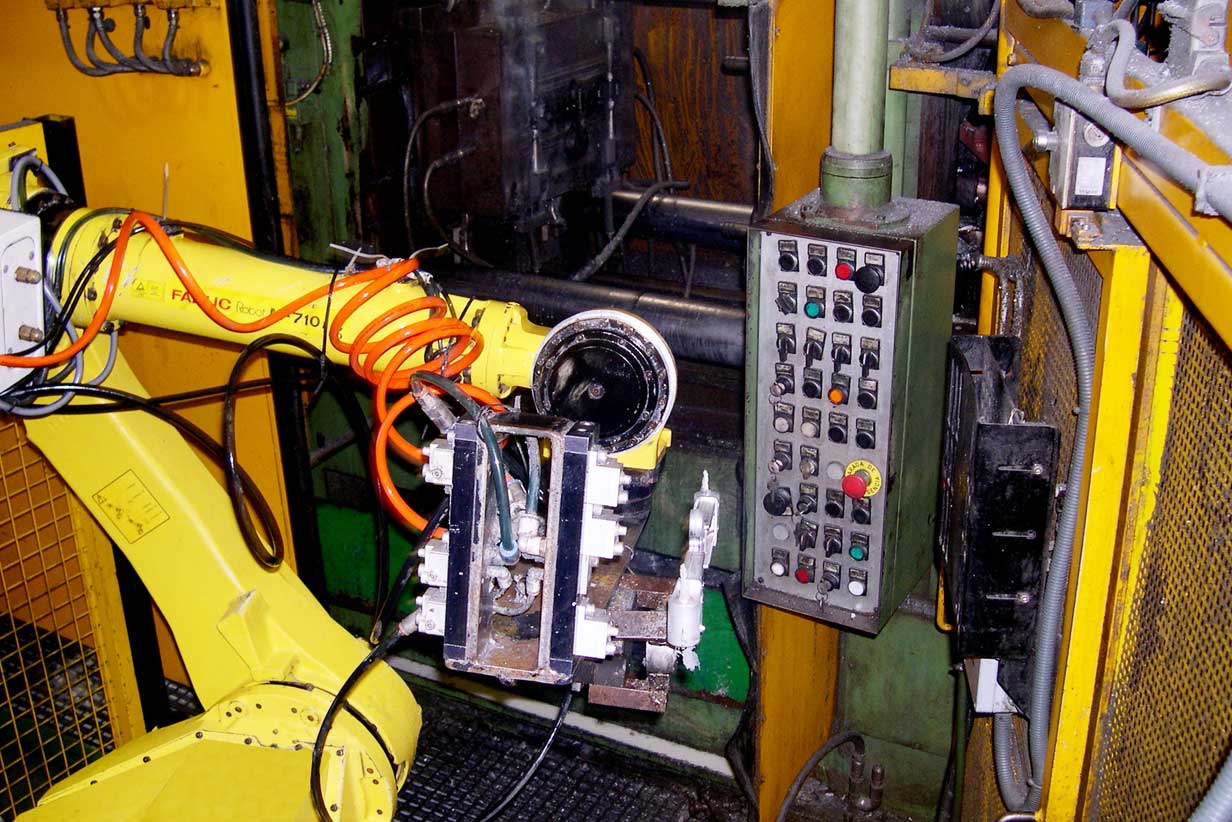
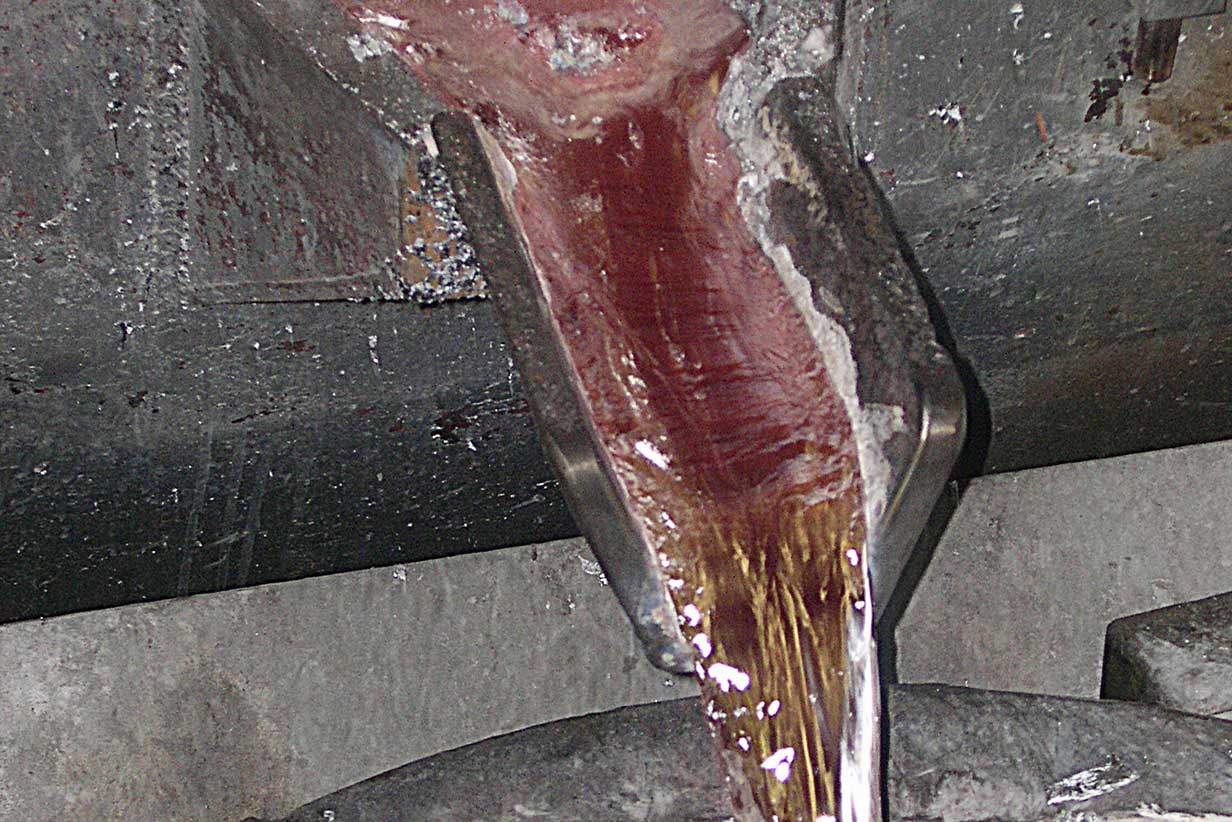
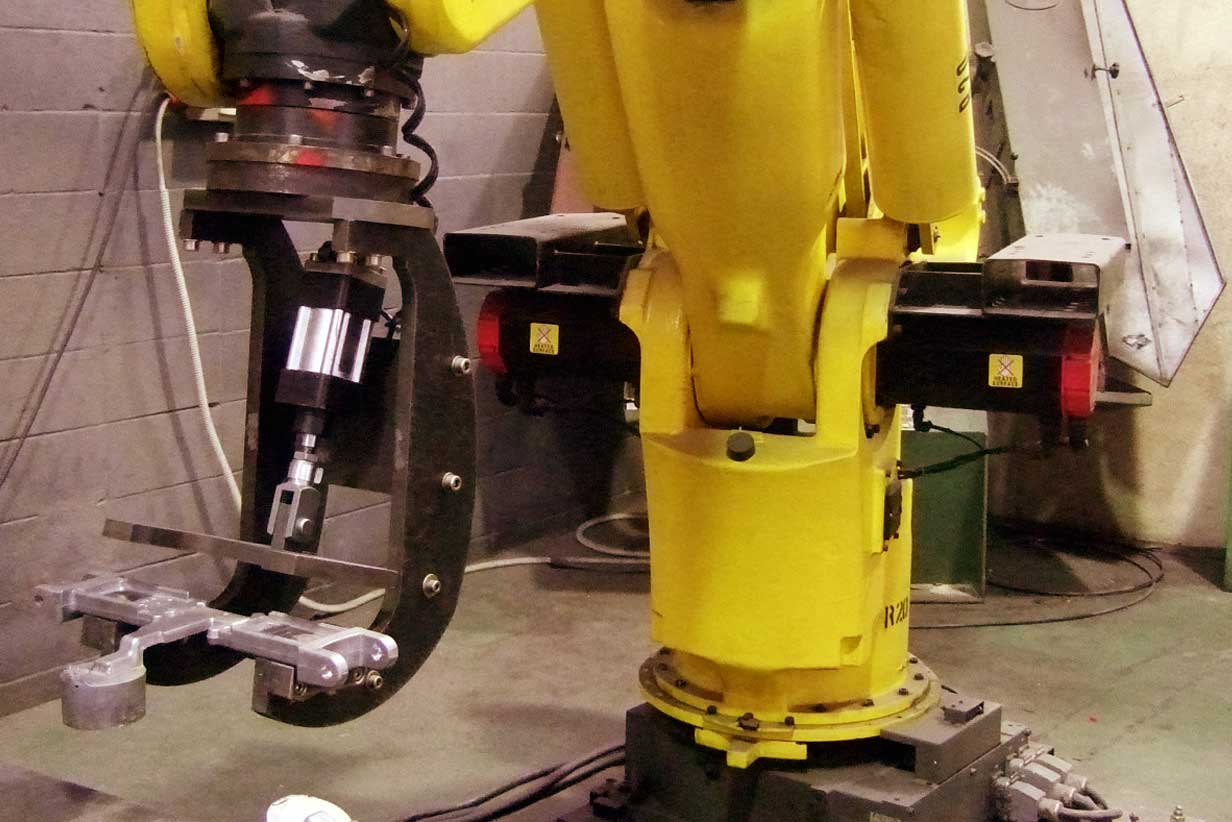
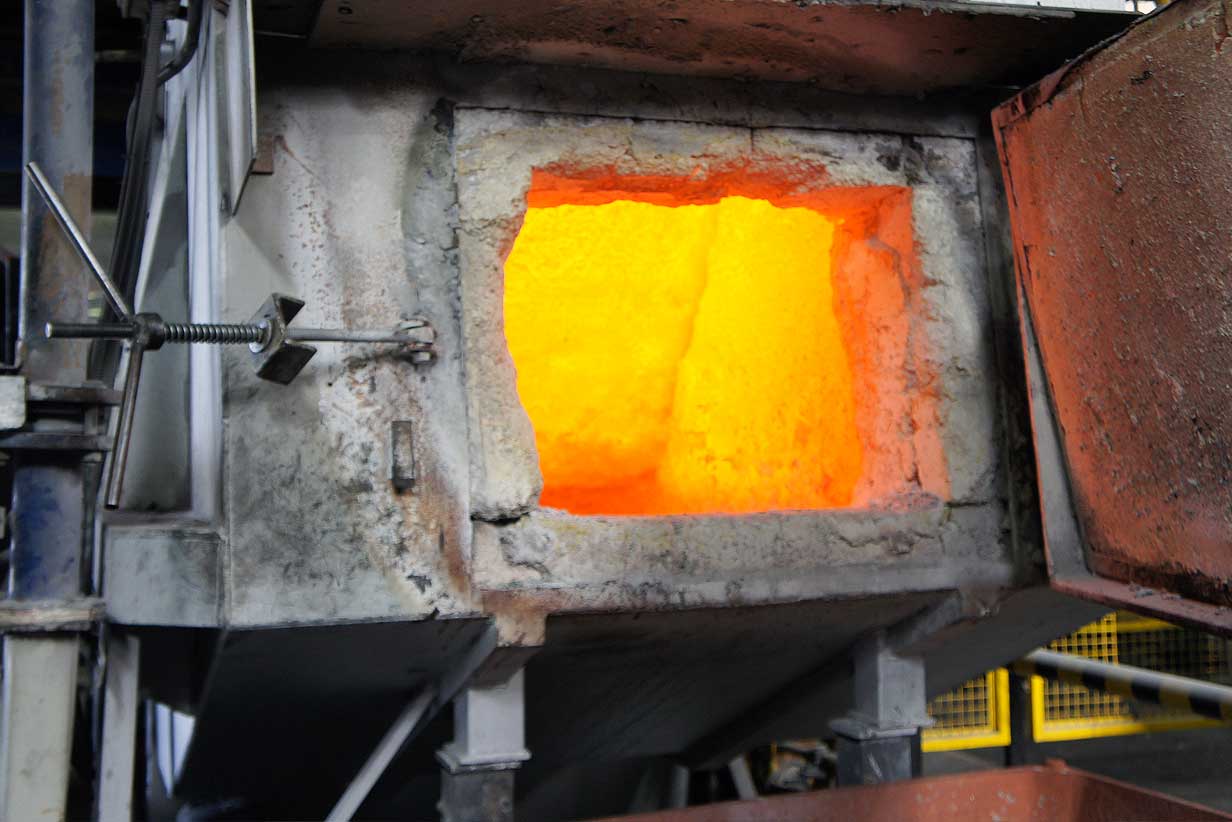
Zamak injection
Zamak is an alloy whose main component is Zinc. The manufacturing process for the parts is the same as for aluminum injection, with the difference that all press components must be kept hot.
The advantage of zamak is a faster production cycle. It allows a reproduction of all the details of the part that will not need to be mechanized.
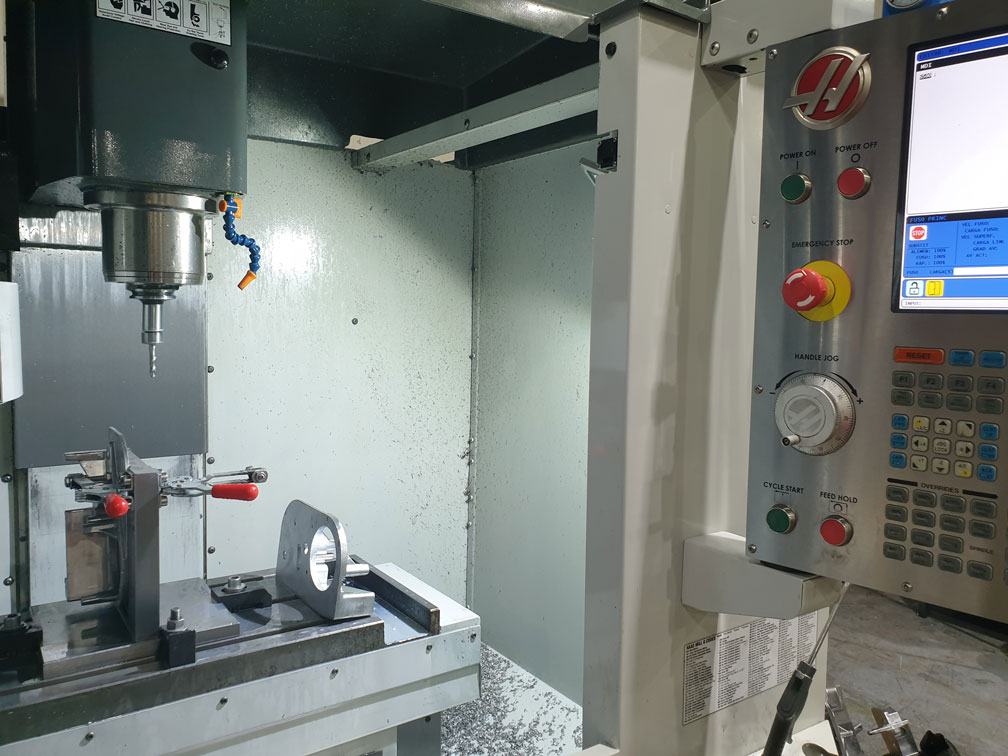
MECHANIZATION
There are mechanization workshops in all production units.
To meet the requirements of our systems, some parts leaving the foundry must pass through machining centers for high mechanical precision.
At this stage we also check the hardware and finishing of the parts before processing and/or painting.
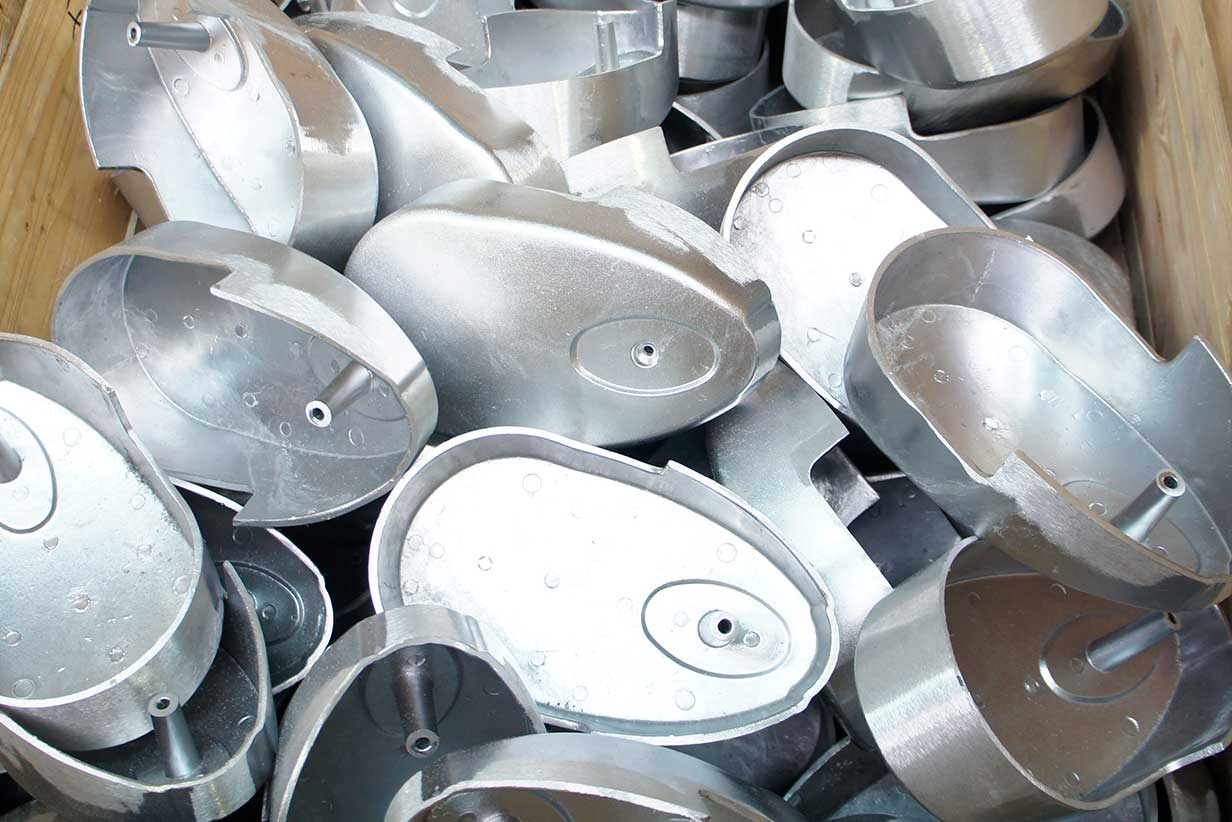
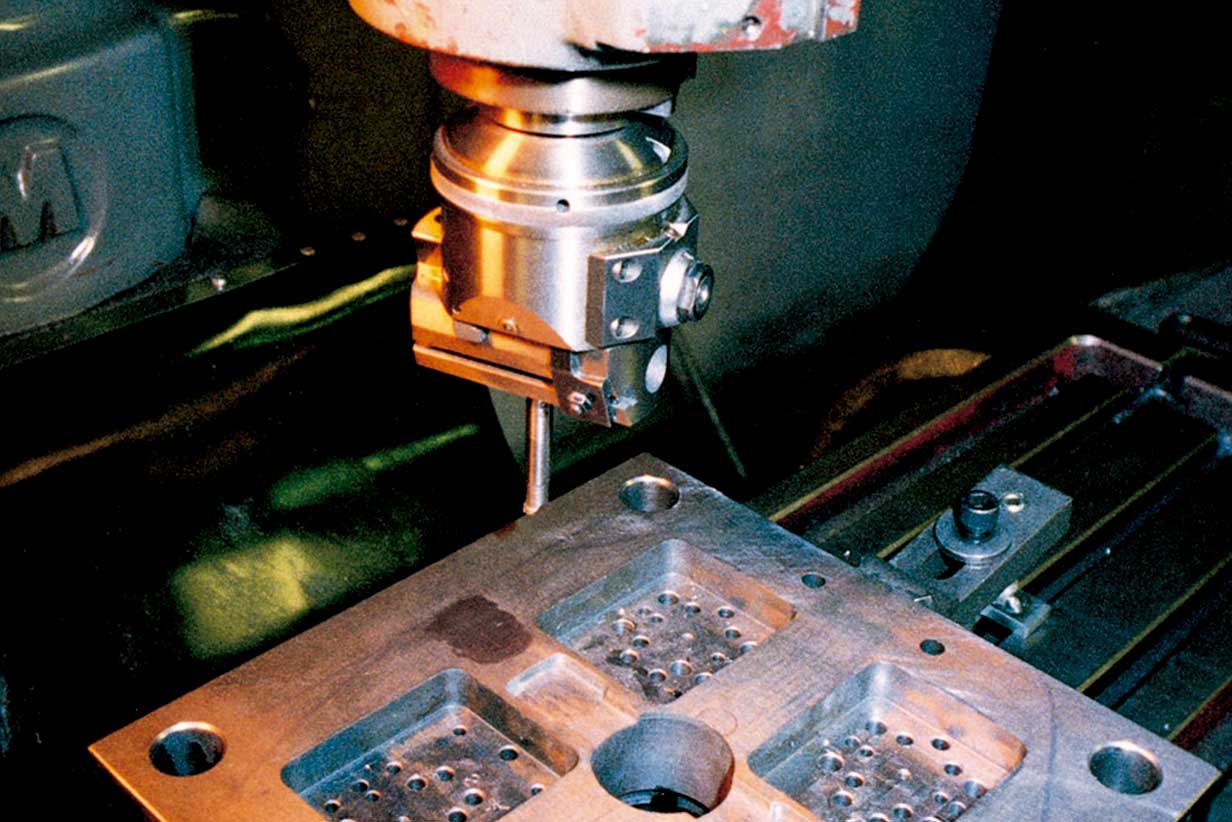
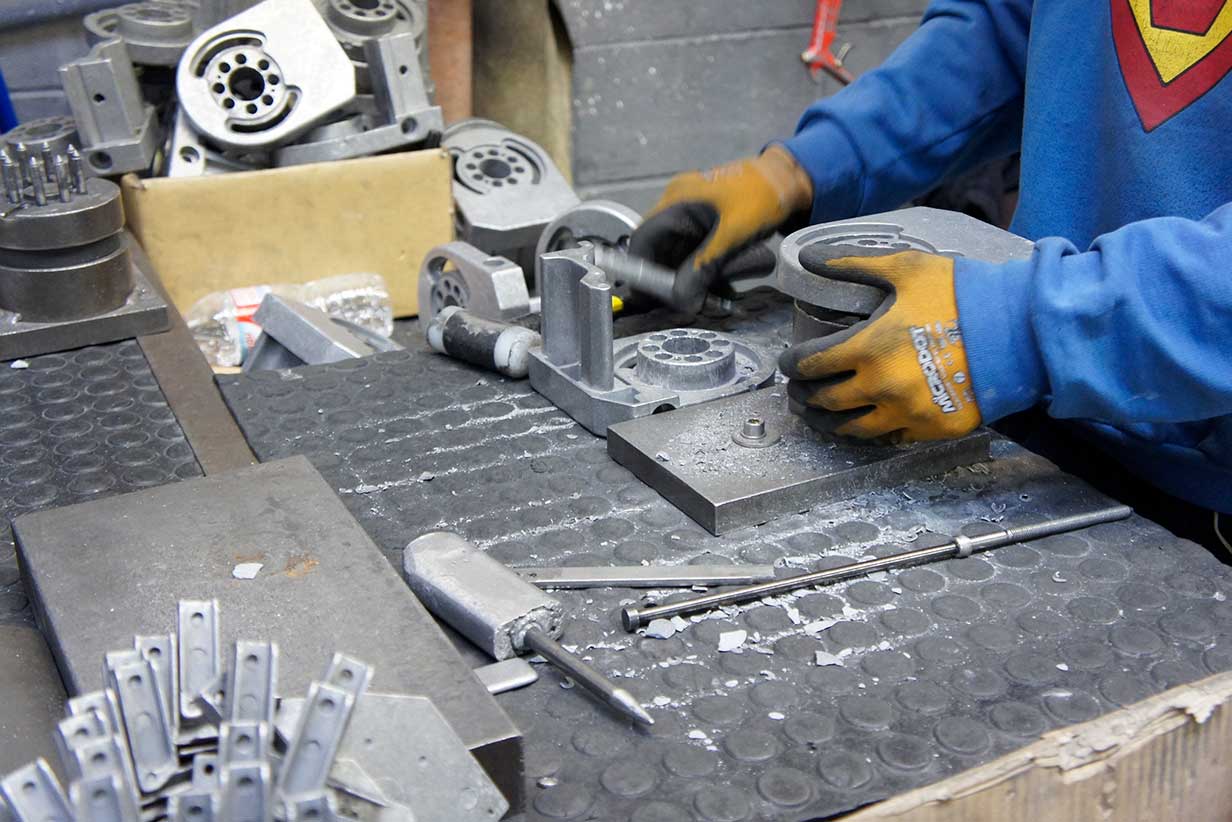
NEW ALUMINIUM ALLOY
Better part strength
In the spirit of improving the quality of our products, our aluminium foundries now use a new aluminium alloy to produce castings.
This alloy contains less iron than conventional alloys but is offset by an increase in manganese content (an iron-like transition metal). The advantage is to provide a material that combines strength and durability, due to its extremely fine grains.
As a result, the alloy increases the mechanical and corrosive resistance of our parts.
After having carried out numerous tests, we have observed a better resistance of our castings with the new alloy which has 35% to 40% more resistance compared to our standard alloy.
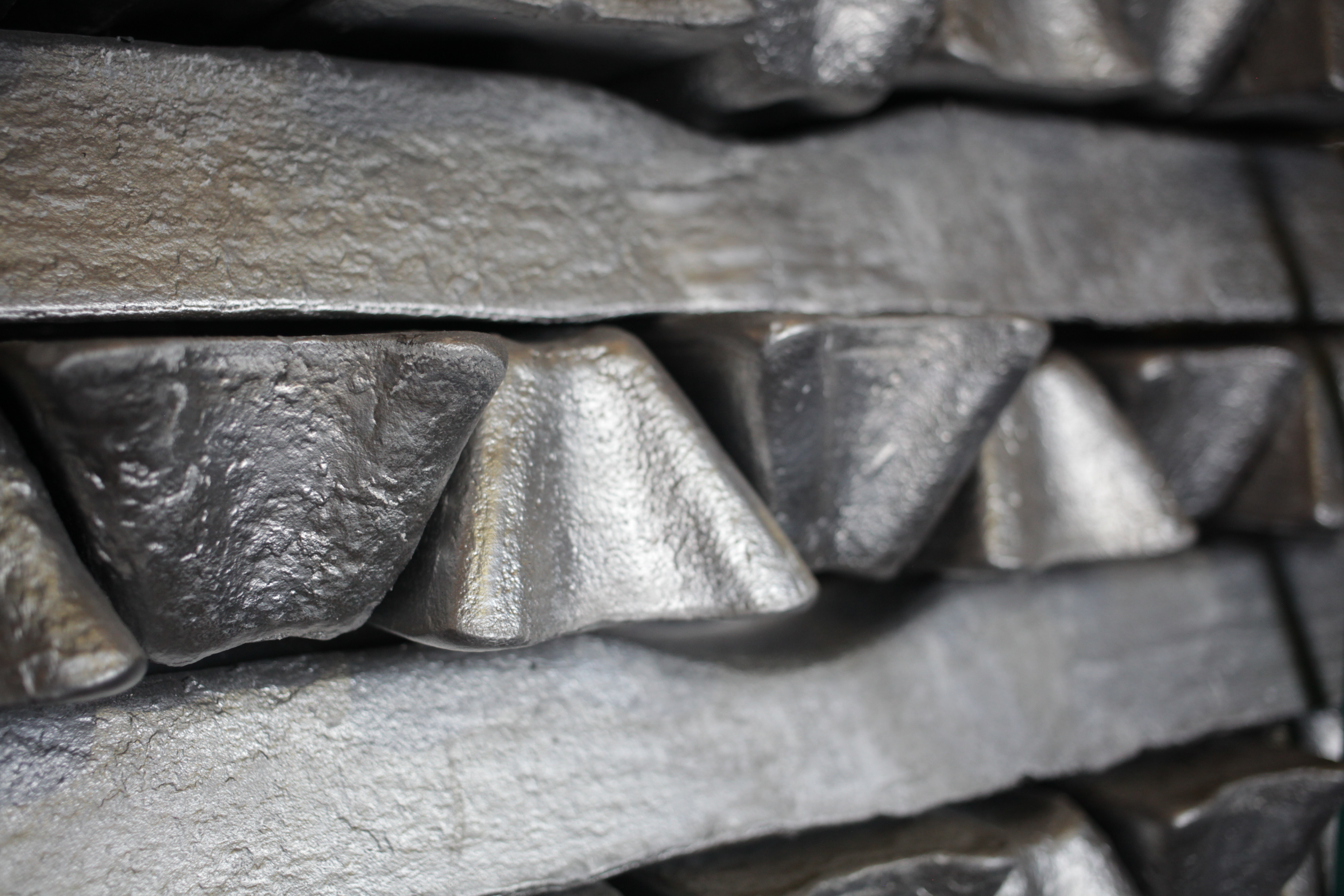